Introducción
Los perfiles de radiador de aleación de aluminio se han convertido en componentes esenciales en la construcción y la industria, gracias a sus características únicas y eficiencia. La producción de estos perfiles comienza con la calidad del lingote y abarca el diseño del molde, la reducción de la fuerza de extrusión y el proceso de extrusión en sí.
Requisitos de Calidad para la Colada de Lingotes
Es crucial que la superficie del lingote sea lisa y libre de segregaciones, arena o barro. La planitud de la cara final del lingote es esencial para evitar problemas durante la extrusión, como la formación de dientes desiguales en el molde o un flujo inconsistente.
Consideraciones sobre Diseño y Material de Moldes
Los moldes para perfiles de radiadores deben ser robustos, especialmente en sus partes más delgadas, para resistir grandes fuerzas de extrusión. El uso de acero de molde de alta calidad, como el H13 o aceros importados de alta calidad, es fundamental. Un tratamiento térmico adecuado asegura la dureza y la tenacidad necesarias en los moldes.
Reducción de la Fuerza de Extrusión
Minimizar la fuerza de extrusión es vital, especialmente al considerar la longitud del lingote y la resistencia a la deformación de la aleación. Se recomienda utilizar lingotes más cortos, especialmente durante las pruebas del molde y la primera extrusión, para garantizar un proceso suave y eficiente.
Optimización del Proceso de Extrusión
El primer ensayo del molde de extrusión es crucial. Se debe comenzar con una presión baja y aumentarla gradualmente, controlando la velocidad de extrusión y la temperatura del molde para evitar bloqueos o flujos desiguales.
Conclusión
Cada paso en la producción de perfiles de radiador de aleación de aluminio es vital para garantizar la calidad y la eficiencia. Desde la colada del lingote hasta el proceso final de extrusión, la atención al detalle y la precisión son esenciales para lograr perfiles de alto rendimiento en la industria moderna.
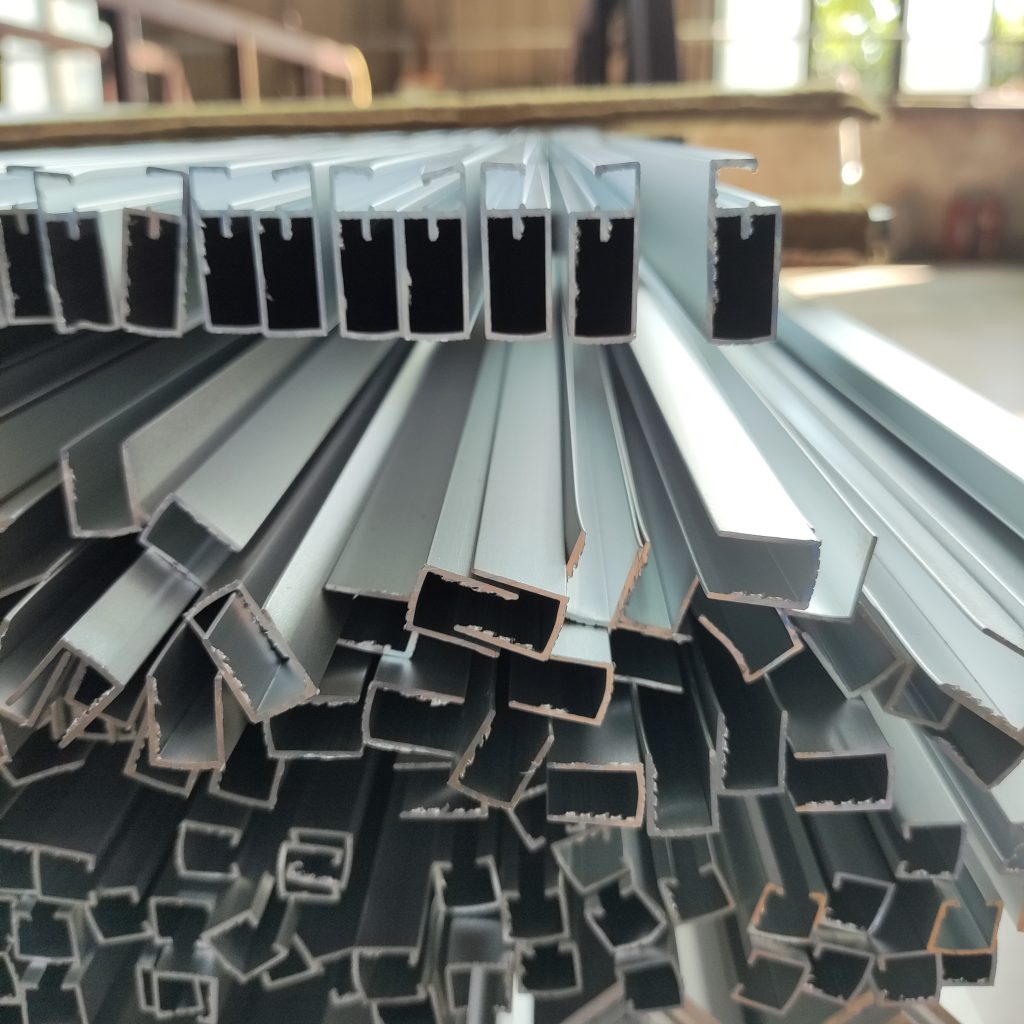